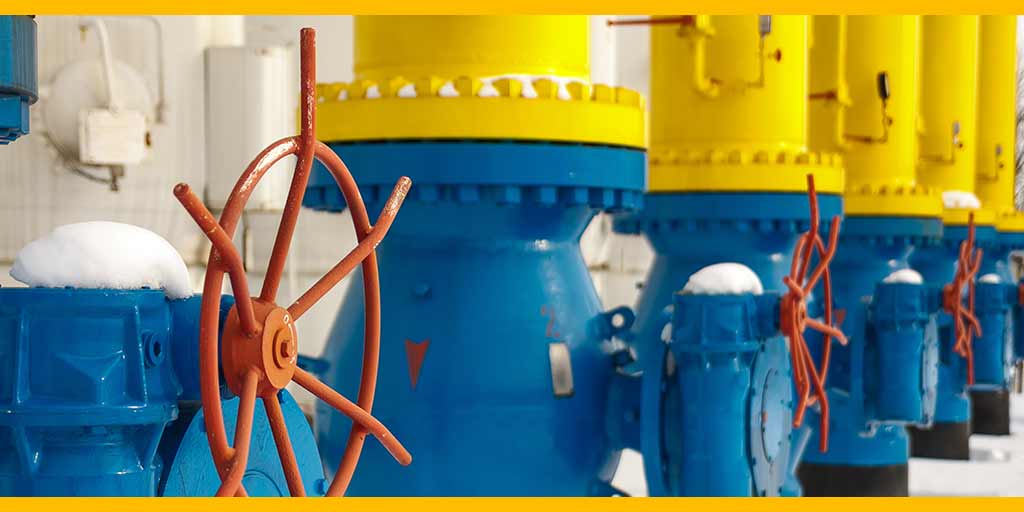
La planificación y ejecución de los trabajos de mantenimiento no es algo que se pueda realizar sin seguir unas normas. Cuando no se ha definido una estrategia a seguir, a menudo nos encontramos con que los trabajos menos agradables, más incómodos o lentos, son los que se quedan aparcados aunque puedan suponer un riesgo. Esto se repite tanto para acciones preventivas como correctivas.
Es imprescindible definir una política de planificación, pero no es tan fácil como puede parecer en un principio. El departamento de mantenimiento en la industria, por ejemplo, está vinculado a otras secciones, de modo que una mala coordinación puede suponer serios inconvenientes. Además, podemos caer en la trampa de pensar que el mantenimiento solo sirve para mantener las máquinas en funcionamiento, así que su única misión es evitar que se pare la producción. Según esta filosofía, detener la producción expresamente para subsanar un fallo es peor que esperar a que sea éste el que provoque la parada de la máquina, así solamente se para cuando no queda más remedio, y podemos justificar que las pérdidas de producción son las mínimas, aunque en realidad suponen mayores daños y tiempo de reparación, sin contar que en algunos casos se retrasa la entrega del producto. Si pensamos así, estamos llevando a la empresa y sus trabajadores a situaciones comprometidas, que pueden suponer serios problemas para la viabilidad del proyecto e incluso para la seguridad de las personas.

El mantenimiento está integrado con la mayoría de departamentos de una empresa: producción, riesgos laborales, calidad, almacén, compras, etc. Esta integración hace que se deban tener en cuenta muchos factores a la hora de definir una política de planificación. Lo que en un principio es conveniente para evitar caídas de producción puede resultar negativo para la calidad o los riesgos laborales, por ejemplo. Dependiendo del tamaño y tipología de la empresa, el número de departamentos y sus relaciones serán diferentes. Para desarrollar una política de gestión eficaz, es necesario valorar todos estos detalles.
Un buen sistema para planificar los trabajos es analizando su nivel de criticidad, que se obtenga a partir de distintos parámetros. Por ejemplo, si cada departamento tuviese una lista con los trabajos de mantenimiento pendientes y tuviese que asignarles un orden de prioridad, seguramente cada uno daría un resultado distinto. La solución completa sería dar distinto peso a cada lista, por ejemplo, siempre es más importante la seguridad que la producción, de modo que la lista del departamento de riesgos tendría más peso que la de producción. El planteamiento es simple, pero llevarlo a la práctica según el ejemplo supondría cientos de reuniones e intercambios de documentación, así que dispararía los costes y reduciría la productividad.
La solución más práctica consiste en automatizar esta toma de decisiones, de modo que simplemente aportando unos datos básicos se puedan ordenar los trabajos según sus riesgos y prioridades. Por ejemplo, FidesGeM utiliza cuatro parámetros para asignar un índice de criticidad a cada trabajo: si hay una función de repuesto disponible, impacto o riesgo en la seguridad, en las operaciones, y en el consumo energético. Con este sencillo método, decimos a la aplicación los riesgos o el impacto que causa la incidencia, y el programa calcula su índice, asignando más peso a unos parámetros que a otros. Mediante ese índice, podemos ordenar los trabajos para ejecutar primero los más críticos. Con este sistema, además, mejoramos el uso de los recursos, porque podemos superar períodos de exceso de carga de trabajo dejando de hacer las acciones con menores riesgos, retomándolas en momentos de menor carga. Como también evitamos incidencias graves, dedicamos menos tiempo a subsanar sus consecuencias, consiguiendo una mayor eficacia, que reflejará estos beneficios en el resto de departamentos.
Y tú, ¿cómo gestionas la planificación de los trabajos?
Deja una respuesta